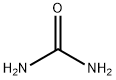
Urea synthesis
- Product Name:Urea
- CAS Number:57-13-6
- Molecular formula:CH4N2O
- Molecular Weight:60.06
The dehydration of ammonium carbamate is appreciable only at temperatures above the melting point (about 150°C) and this reaction can only proceed if the combined partial pressure of ammonia and carbon dioxide exceeds the dissociation pressure of the ammonium carbamate (about 10 MPa at 160°C and about 30 MPa at 200°C). Thus commercial processes are operated in the liquid phase at 160-220°C and 18-35 MPa (180-350 atmospheres). Generally, a stoichiometric excess of ammonia is employed, molar ratios of up to 6: 1 being used. The dehydration of ammonium carbamate to urea proceeds to about 50-65% in most processes. The reactor effluent therefore consists of urea, water, ammonium carbamate and the excess of ammonia. Various techniques are used for separating the components. In one process the effluent is let down in pressure and heated at about 155°C to decompose the carbamate into ammonia and carbon dioxide. The gases are removed and cooled. All the carbon dioxide present reacts with the stoichiometric amount of ammonia to re-form carbamate, which is then dissolved in a small quantity of water and returned to the reactor. The remaining ammonia is liquefied and recycled to the reactor. Fresh make-up ammonia and carbon dioxide are also introduced into the reactor. Removal of ammonium carbamate and ammonia from the reactor effluent leaves an aqueous solution of urea. The solution is partially evaporated and then urea is isolated by recrystallization. Ammonium carbamate is very corrosive and at one time it was necessary to use silver-lined equipment but now satisfactory alloy steel plant is available.
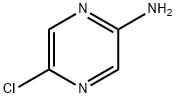
33332-29-5
245 suppliers
$14.00/1g
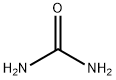
57-13-6
692 suppliers
$5.00/5g
Yield:57-13-6 220 mg
Reaction Conditions:
Stage #1: 2-amino-5-chloropyrazinewith bis(trichloromethyl) carbonate;N-ethyl-N,N-diisopropylamine in dichloromethane;ethyl acetate at 0; for 0.25 h;
Stage #2: with dmap in dichloromethane;ethyl acetate at 0; for 0.0833333 h;
Stage #3: with methyl 2-aminoisobutyrate hydrochloride at 0; for 0.5 h;
Steps:
Intermediate 5 route 1 3-(5-chloropyrazin-2-yl)-5.5-dimethyl-imidazolidine-2,4-dione
To a solution of bis(trichloromethyl) carbonate (950mg, 3.20mmol) in ethyl acetate (30ml_) at 0°C a solution of 5-chloropyrazin-2-amine (0.75g, 5.79mmol)/N,N-diisopropylethylamine (6.05ml, 34.74mmol) in ethyl acetate (12ml_) was added dropwise and the reaction mixture was stirred for 15 minutes at the same temperature. Maintaining the reaction mixture at 0°C, vacuum was applied (5 minutes) in order to remove the excess of phosgene. A solution of 4- (dimethylamino)pyridine (710mg, 5.81 mmol) in ethyl acetate (8ml_)/ dichloromethane (2ml_) was added and the reaction mixture was stirred for 5 minutes at the same temperature. Then, methyl 2-amino-2-methyl-propanoate hydrochloride (1.4g, 9.1 mmol) was added at 0°C and the reaction mixture was stirred for 30 minutes at the same temperature. The reaction was quenched with a solution 0.2 N of HCI (100 ml) and the two phases were separated. The organic layer was washed with brine (100 ml), dried over Na2SC>4, filtered and evaporated affording the urea intermediate. The urea was dissolved in dichloromethane (20ml_) and at 0°C sodium methoxide (315mg, 5.83mmol) was added. The reaction mixture was stirred 15 minutes at the same temperature; the reaction was quenched with a saturated solution of NH CI to allow the pH to reach 3-4. The mixture was extracted with ethyl acetate (50 ml); phases were separated, and the organic layer was washed with brine (50 ml), dried over Na2SC>4, filtered and evaporated. The residue were purified by reverse phase flash chromatography (Biotage System) on C-18 phase using a SNAP 30g as column and WaterAcetonitrile from 95:5 to 40:60 as eluent. The appropriate fractions were combined and evaporated to dryness affording 3-(5-chloropyrazin-2-yl)-5,5-dimethyl- imidazolidine-2,4-dione (220mg) as a pale brown solid. LC/MS: QC_3_M I N : Rt = 1.649 min; m/z 241 & 243 [M+H]+.
References:
WO2021/156584,2021,A1 Location in patent:Page/Page column 49-50
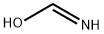
60100-09-6
0 suppliers
inquiry
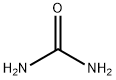
57-13-6
692 suppliers
$5.00/5g
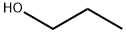
71-23-8
744 suppliers
$12.00/100g
201230-82-2
1 suppliers
inquiry
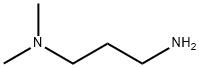
109-55-7
336 suppliers
$14.00/25mL
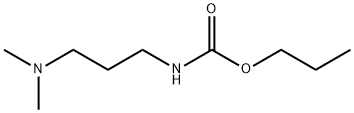
24579-73-5
150 suppliers
$56.10/250mg
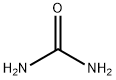
57-13-6
692 suppliers
$5.00/5g

124-38-9
122 suppliers
$214.00/14L
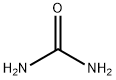
57-13-6
692 suppliers
$5.00/5g

420-04-2
338 suppliers
$15.00/25g
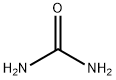
57-13-6
692 suppliers
$5.00/5g