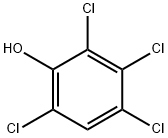
2,3,4,6-TETRACHLOROPHENOL synthesis
- Product Name:2,3,4,6-TETRACHLOROPHENOL
- CAS Number:58-90-2
- Molecular formula:C6H2Cl4O
- Molecular Weight:231.89
Yield:58-90-2 10% ,87-86-5 80%
Reaction Conditions:
with chlorine;nickel;aluminum (III) chloride at 90 - 180; for 4.16667 - 4.66667 h;Product distribution / selectivity;
Steps:
Experimental Details-Chlorine Flow Rate Termination and Addition of Metal; For the following experiments, pentachlorophenol was formed by the AlCl3-catalyzed (0.25 wt %) chlorination of trichlorophenol in a round bottom flask. Chlorine gas continuously bubbled through the molten reaction medium. As chlorination occurred, the melting point of the mixture increased, so the reactor temperature was increased to keep it a few degrees above the melting point. Samples of the reaction mixture were withdrawn periodically and analyzed for chlorophenols (by gas chromatography) and for microcontaminants (by bioassay). At the end of the experiments, the reactor contents are poured into a disposable aluminum pan to cool and solidify. This post-reaction product was often analyzed. Acetone, aqueous HNO3 solution, and methanol were used successively to clean the reactor after each experiment. The chlorine flow in all of the experiments was terminated when the reactor temperature reached 180° C. This operation mode leaves a small amount of tetrachlorophenol unconverted in the reactor. Varying Time of Nickel Addition Three experiments were performed in which the time at which nickel powder (about 0.75 g≈2500 ppm) was added was the variable. In all cases, the chlorine flow to the reactor was replaced with N2 when the reactor temperature reached 180° C. The results shown in FIGS. 9A may be compared with the other experiments terminating chlorine flow at 180° C. The conditions of the experiments are similar except for the addition of Ni powder at 180° C. Results from seven different experiments that stopped chlorine flow at 180+/-3° C. were used to calculate mean TEQ concentrations of 0.38+/-0.12 ppm for the sample at the maximum tetrachlorophenol yield, 0.53+/-0.14 ppm for the last sample taken from the reactor, and 0.59+/-0.18 ppm for the post-reaction sample from the aluminum pan. The uncertainties shown here are the standard deviations about the mean. The TEQ concentrations in FIG. 9A are slightly higher than the means given above, but they are within the range of TEQ values seen experimentally from experiments with chlorine flow stopping at about 180° C. without added Ni. As such, the addition of Ni near the end of the run does not appear to have an effect on the TEQ concentrations. The results shown in FIGS. 9B and 9C indicate that adding Ni earlier in the synthesis does seem to have benefits. In FIG. 9B, the Ni was added when the reactor reached about 160° C., and in FIG. 9C, the Ni was added (along with the catalyst) at 90° C. In both cases, the TEQ concentrations were around 0.3 ppm in all samples, and there was no increase in TEQ concentration after the maximum tetrachlorophenol yield was reached. Collectively these results suggest that Ni powder does not substantially alter the TEQ concentration present at the maximum tetrachlorophenol yield, and that it does not substantially reduce the TEQ concentration much when added near the end of the run. Rather, the results indicate that nickel inhibits the TEQ concentration increase that had occurred in other runs between the maximum tetrachlorophenol yield and the final pentachlorophenol product. Three additional experiments were performed to check the reproducibility of these results. FIGS. 10A and 10B show the chlorophenol yields and TEQ concentrations obtained at the same experimental conditions used to generate FIG. 9C. The TEQ values were about 0.38 ppm at the maximum tetrachlorophenol yield, and about 0.5 ppm for the last sample withdrawn from the reactor. The TEQ concentrations for the post-reaction pentachlorophenol samples taken from the aluminum pan were about 0.46 ppm and about 0.65 ppm. FIG. 10C illustrates the results from an experiment where the chlorine flow and the temperature ramp were stopped at 180° C. The TEQ concentration was about 0.25 ppm for the last sample from the reactor, and about 0.34 ppm for the post-reaction pentachlorophenol product. These TEQ concentrations are similar to those shown in FIG. 9C, and thus confirm that the TEQ reductions obtained by adding Ni at the start of the synthesis reaction are reproducible. The accuracy of the cleaning procedure was verified by periodically doing experiments with no added Ni and verifying that pentachlorophenol with higher TEQ was produced. For example, one such run with no added Ni led to a TEQ concentration at the maximum tetrachlorophenol yield of 0.79 ppm and a TEQ concentration in the final post-reaction sample of 2.4 ppm. These values are higher than those that appear for runs with added Ni. Additional Catalyst As catalyst concentrations greater than 0.25 wt. % appeared to have a modest effect on reducing the TEQ concentration in the pentachlorophenol product (see FIG. 3A), experiments were conducted to test the behavior of additional AlCl3 catalyst (0.75 wt. % and 1.50 wt. %) when nickel was also added. In each of these experiments, the temperature ramp was terminated at 180° C., where the chlorine flow was stopped. The results from a run with the 0.25 wt. % catalyst concentration appears in FIG. 10C. FIGS. 11A and 11B show the results for the experiments with 0.75 wt. % catalyst and 1.5 wt. % catalyst, respectively. In spite of the different catalyst concentrations, the final samples taken from the reactor had similar TEQ concentrations (about 0.25, about 0.13, and about 0.23 ppm for 0.25, 0.75 and 1.5 wt. % catalyst, respectively). The TEQ concentrations in the post-reaction samples taken from the aluminum pans were also similar (about 0.34, about 0.25, and about 0.38 ppm, for 0.25, 0.75 and 1.5 wt. % catalyst, respectively). The results indicate that running the synthesis at catalyst concentrations higher than 0.25 wt. % has little or no appreciable effect on the TEQ concentrations when Ni is also added to the reactor. Varying Nickel Concentration The effects of adding more and less nickel during the pentachlorophenol synthesis were tested. FIG. 12A shows the results from a synthesis experiment with 5000 ppm nickel added. The TEQ concentrations for the last sample from the reactor and for the post-reaction sample were about 0.26 ppm and about 0.44 ppm, respectively. These values do not differ appreciably from the TEQ levels obtained with less Ni, which indicates that the higher Ni level did not appear to reduce the TEQ level any further. FIG. 12B shows the results from a synthesis using about 1250 ppm nickel. About 84% pentachlorophenol was produced at 225 minutes, with 12% tetrachlorophenol and about 0.33 ppm TEQ. About 90% pentachlorophenol was obtained at 234 minutes and 180° C., with 5% tetrachlorophenol residual and about 0.71 ppm TEQ. The pentachlorophenol yield in the post-reaction sample was about 89% with 5% tetrachlorophenol and about 0.37 ppm TEQ. FIG. 12C shows the results from a synthesis using about 833 ppm nickel. In the last sample from the reactor (taken at 180° C. and 255 minutes), the pentachlorophenol yield was about 90%, with 7% tetrachlorophenol remaining and about 0.37 ppm TEQ concentration. The TEQ concentration in the post-reaction pentachlorophenol sample, where the pentachlorophenol yield was about 87% with 6% tetra, was about 0.39 ppm. FIG. 12D shows results from a synthesis using about 100 ppm nickel. The TEQ concentrations were about 0.4 ppm. The results shown in FIGS. 12B-12D indicate that using about 100 ppm, about 833 ppm, or about 1250 ppm of nickel provides substantially similar TEQ concentrations (from about 0.3 to about 0.4 ppm) in the final pentachlorophenol product as using 2500 ppm nickel.
References:
The Regents of the University of Michigan US2007/225529, 2007, A1 Location in patent:Page/Page column 5-6
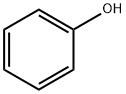
108-95-2
767 suppliers
$14.00/25g
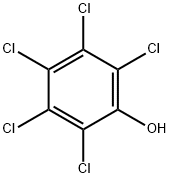
87-86-5
0 suppliers
$23.50/48692
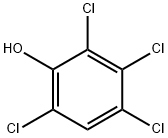
58-90-2
76 suppliers
$47.20/48264
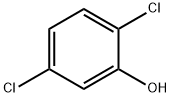
583-78-8
249 suppliers
$15.00/250 mg
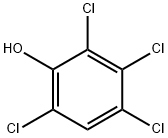
58-90-2
76 suppliers
$47.20/48264
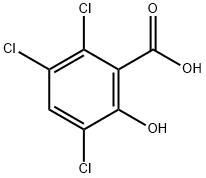
40932-60-3
235 suppliers
$29.00/25g
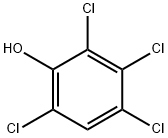
58-90-2
76 suppliers
$47.20/48264
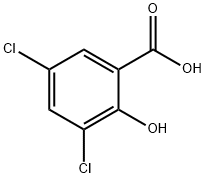
320-72-9
243 suppliers
$16.00/5 g
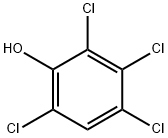
58-90-2
76 suppliers
$47.20/48264