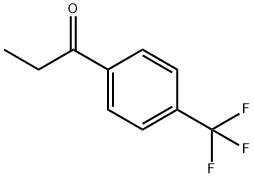
4'-(TRIFLUOROMETHYL)PROPIOPHENONE synthesis
- Product Name:4'-(TRIFLUOROMETHYL)PROPIOPHENONE
- CAS Number:711-33-1
- Molecular formula:C10H9F3O
- Molecular Weight:202.17
Yield: 34.5 %Chromat.
Reaction Conditions:
Stage #1:o-trifluoromethylphenyl bromide with ethylmagnesium bromide;magnesium;lithium chloride in tetrahydrofuran;ethyl bromide at 45 - 50; for 5 h;Inert atmosphere;
Stage #2:propionic acid anhydride in tetrahydrofuran;ethyl bromide;toluene at 20 - 30; for 2 h;Inert atmosphere;
Steps:
3
General procedure: To a 200 ml-four-necked flask with a thermometer,75.0 g of tetrahydroffiran (1.04 mol; manufactured by Nacalai Tesque, Inc.), 5.1 g of magnesium powder (0.208 mol; manufactured by Chuo-kosan), 1.7 g of LiC1 (0.04 mol; manufactured by Nacalai Tesque, Inc.) were placed and the mixture was stirred while the inside of the system was substituted with a nitrogen gas. To this, 0.5 g of 1 mol/L ethylmagnesium bromide THF solution (manufactured by Tokyo Chemical Industry Co., Ltd.) was added and water in the system was removed. Subsequently, 0.44 g of ethyl bromide (0.004 mol; manufactured by Wako Pure Chemical Industries, Ltd.) was added thereto. The mixture was stirred for a while; and the generation of heat was confirmed. Subsequently, 36.1 g of o-chlorobenzotrifluoride (0.2 mol; manufactured by Wako Pure Chemical Industries, Ltd.) was gradually added dropwise, while the temperature of the reaction solution was kept at 45 to 50° C. After the completion of the dropwise addition, the mixture was allowed to mature while stirred at 45° C. for five hours, thereby obtaining a Grignard reagent solution.10043] Next, to a 200 ml-four-necked flask with a thermometer, 30.6 g of acetic anhydride (0.3 mol; manufactured by Wako Pure Chemical Industries, Ltd.), 10.8 g of toluene (0.3 fold by weight/o-chlorobenzotrifluoride: manufactured by Wako Pure Chemical Industries, Ltd.) were placed and the mixture was stirred in a water bath while the inside of the system was substituted with a nitrogen gas. To this, the above Grignard reagent solution was added dropwise while the temperature of the reaction solution was controlled so as to be 20 to 30° C. The entire volume of the Grignard reagent solution was added dropwise and then the mixture was stirred at 25° C. for two hours. After the completion of the stirring, the temperature of the reaction solution was decreased to room temperature; and 39.2 g of 3% hydrogen chloride aqueous solution was gradually added dropwise thereto in a water bath. Afier the dropwise addition, the hydrolysis was completed by stirring for one hour. After the hydrolysis, the stirring was stopped; and the resultant was lefi to stand for separation, thereby obtaining an oil phase containing o-trifluoromethyl acetophenone. The obtained oil phase was analyzed by a gas chromatography method (GC) and as a result, the yield of 2’-trifluoromethyl acetophenone reaction was 82.7% (based on the raw material, o-chlorobenzotrifluoride). A reaction was carried out in the same manner as described in Example 1 except that 36.1 g (0.2 mol) of o-chlorobenzotrifluoride was altered to 45.0 g (0.2 mol) of o-bromobenzotrifluoride in Example 1. The obtained oil phase was analyzed by a gas chromatography method; and as a result, the yield of 2’-tri- fluoromethyl acetophenone reaction was 85.5% (based on the raw material, o-bromobenzotrifluoride). [0054] A reaction was carried out in the same manner as described in Comparative Example 1 except that 45.0 g (0.2 mol) of m-bromobenzotrifluoride was altered to 45.0 g (0.2 mol) of p-bromobenzotrifluoride in Comparative Example 1. The obtained oil phase was analyzed by a gas chromatography method; and as a result, the yield of 4’-trifluoromethyl acetophenone reaction was 40.0% (based on the raw material, p-bromobenzotrifluoride). [0055] A reaction was carried out in the same manner as described in Comparative Example 2 except that 30.6 g (0.3 mol) of acetic anhydride was altered to 39.0 g (0.3 mol) of propionic anhydride in Comparative Example 2. The obtained oil phase was analyzed by a gas chromatography method; and as a result, the yield of 4’-trifluoromethyl propiophenone was 34.5% (based on the raw material,p-bromobenzotrifluoride).
References:
Toray Fine Chemicals Co., Ltd.;Nakatani, Jiro;Nozoe, Tatsuhiro US2017/88499, 2017, A1 Location in patent:Paragraph 0042; 0043; 0044; 0045; 0046; 0047; 0055
![1-[4-(TRIFLUOROMETHYL)PHENYL]PROPAN-1-OL](/CAS/GIF/67081-98-5.gif)
67081-98-5
57 suppliers
$10.00/100mg
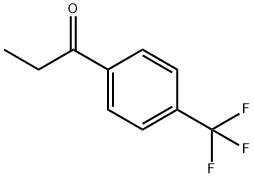
711-33-1
125 suppliers
$14.00/1g
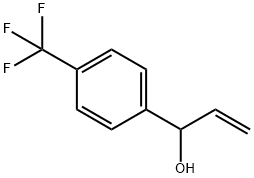
149946-79-2
1 suppliers
inquiry
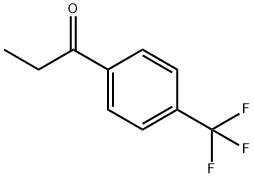
711-33-1
125 suppliers
$14.00/1g
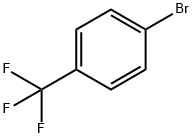
402-43-7
433 suppliers
$6.00/10g
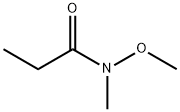
104863-65-2
76 suppliers
$16.00/250mg
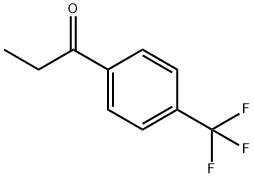
711-33-1
125 suppliers
$14.00/1g