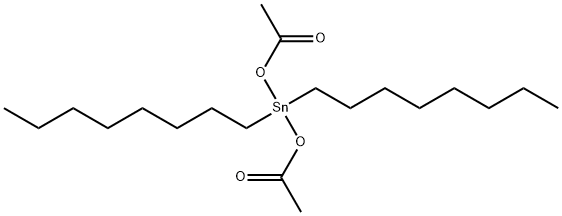
DI-OCTYL TIN DIACETATE synthesis
- Product Name:DI-OCTYL TIN DIACETATE
- CAS Number:17586-94-6
- Molecular formula:C20H40O4Sn
- Molecular Weight:463.24
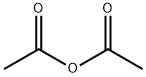
108-24-7
5 suppliers
$14.00/250ML

870-08-6
190 suppliers
$23.30/25g
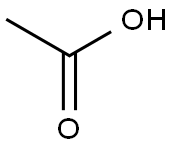
64-19-7
1535 suppliers
$10.00/25ML
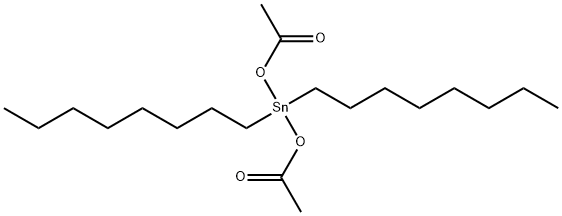
17586-94-6
17 suppliers
inquiry
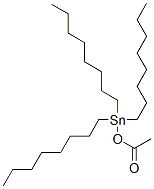
919-28-8
2 suppliers
inquiry
Yield:-
Reaction Conditions:
Stage #1:dioctyltin(IV) oxide with 2-Ethylhexyl alcohol at 180;Inert atmosphere;
Stage #2:acetic anhydride;acetic acid at 50; for 2 h;Product distribution / selectivity;
Steps:
27.1; 27.2
Example 27; Step (27-1): Recovery of Composition of Deactivated Forms Formed Accompanying Production of Dialkyl Tin Catalyst; 562 g (1.56 mol) of dioctyl tin oxide, 3015 g (23.2 mol) of 2-ethyl-1-hexanol and a stirrer for stirring were placed in a 5 L volumetric four-mouth flask equipped with a vacuum controller, a condenser connected to vacuum pump and a Dean-Stark tube. After replacing the inside of the system with nitrogen, the flask was immersed in an oil bath heated to 180°C and stirring was started. After continuing to heat for about 5 hours while removing the distillate, the pressure was gradually reduced, after which a low boiling point component was further distilled off for about 5 hours with the pressure inside the system at from 76 to 30 kPa. The flask was cooled after new distillate was no longer observed. 778.3 g of a reaction liquid were obtained in the flask and as a result of analyzing by 1H- and 119Sn-NMR, the reaction liquid was found to contain 40.1 wt% of 1,1,3,3-di-n-octyl-tetra(2-ethylhexyloxy) tin, 16.9 wt% of di-n-octyl-bis(2-ethylhexyloxy) tin and 25.8 wt% of tri-n-octyl(2-ethylhexyloxy) tin.; Step (27-2): Substituent Exchange Reaction of Deactivated Forms of Dialkyl Tin Catalyst; 775.8 g of the reaction liquid obtained in step (27-1), 298.1 g of acetic acid and 544.3 g of acetic anhydride were placed in a 2 L pear-shaped flask, and the flask was placed in a water bath controlled to 50°C followed by stirring for 2 hours. The flask was attached to a rotary evaporator to which was connected an oil bath equipped with a temperature controller, a vacuum pump and a vacuum controller. The purge valve outlet of the rotary evaporator was connected to a line containing nitrogen gas flowing at normal pressure. After replacing the inside of the system with nitrogen, the temperature of the oil bath was set to 50°C, the flask was immersed in the oil bath and rotation of the rotary evaporator was started. After distilling off the excess acetic acid and acetic anhydride under reduced pressure at 0.1 kPa, 685.9 g of a residue was obtained in the flask. Based on the results of 1H- , 13C- and 119Sn-NMR analyses, the residue was found to be a mixture containing tri-n-octyl acetoxy tin and di-n-octyl diacetoxy tin, and the content of tri-n-octyl acetoxy tin in the mixture was 25.8 wt%, while the content of di-n-octyl diacetoxy tin was 58.9 wt%.
References:
Asahi Kasei Chemicals Corporation EP2078724, 2009, A1 Location in patent:Page/Page column 54
![Ethanamine, N-[(3,5-dichlorophenyl)methylene]-2,2-diethoxy-](/CAS/20210305/GIF/1000210-73-0.gif)
1000210-73-0
0 suppliers
inquiry
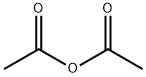
108-24-7
5 suppliers
$14.00/250ML
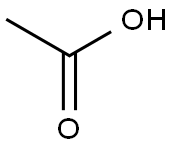
64-19-7
1535 suppliers
$10.00/25ML
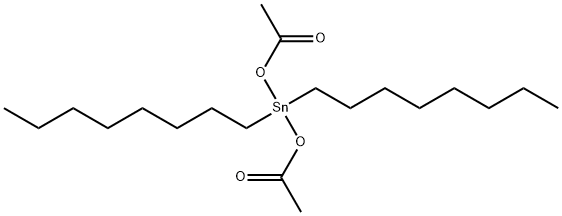
17586-94-6
17 suppliers
inquiry
![Ethanamine, N-[(3,5-dichlorophenyl)methylene]-2,2-diethoxy-](/CAS/20210305/GIF/1000210-73-0.gif)
1000210-73-0
0 suppliers
inquiry
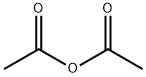
108-24-7
5 suppliers
$14.00/250ML
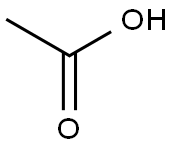
64-19-7
1535 suppliers
$10.00/25ML
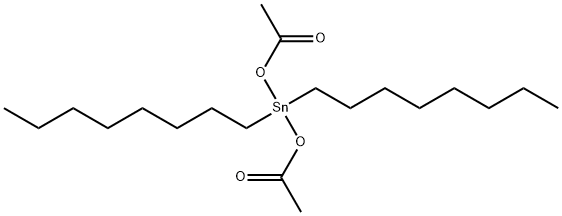
17586-94-6
17 suppliers
inquiry
![Ethanamine, N-[(3,5-dichlorophenyl)methylene]-2,2-diethoxy-](/CAS/20210305/GIF/1000210-73-0.gif)
1000210-73-0
0 suppliers
inquiry
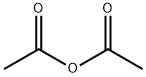
108-24-7
5 suppliers
$14.00/250ML
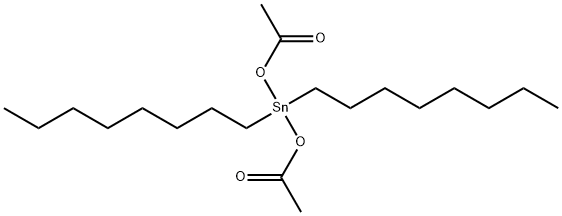
17586-94-6
17 suppliers
inquiry
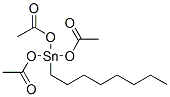
77928-59-7
1 suppliers
inquiry