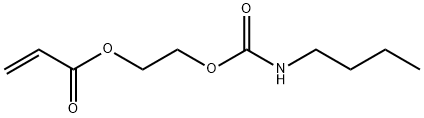
2-[[(BUTYLAMINO)CARBONYL]OXY]ETHYL ACRYLATE synthesis
- Product Name:2-[[(BUTYLAMINO)CARBONYL]OXY]ETHYL ACRYLATE
- CAS Number:63225-53-6
- Molecular formula:C10H17NO4
- Molecular Weight:215.25

13105-54-9
12 suppliers
inquiry
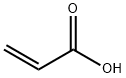
79-10-7
688 suppliers
$20.50/500ml
![2-[[(BUTYLAMINO)CARBONYL]OXY]ETHYL ACRYLATE](/CAS/GIF/63225-53-6.gif)
63225-53-6
34 suppliers
$63.89/100ml
Yield:-
Reaction Conditions:
with hypophosphorous acid;4-methoxy-phenol;toluene-4-sulfonic acid in toluene at 70; for 6 h;Reduced pressure;
Steps:
2R.1 Comparative example 2R; Preparation of n-butyl acryloyloxy ethyl carbamate by the Direct Esterification Method.; 1/Acrylation of 2-hydroxyethyl butyl carbamate by direct esterification
Direct esterification of 2-hydroxyethyl butyl carbamate prepared such as described in Example 1 (1/) was carried out adding to a double-wall glass reactor (1. 5 1) fitted with an agitator, a thermometer, a gas inlet tube, a connection to vacuum and an azeotropic distillation column having a Dean-Stark separator at its overhead, 332 g (2 moles) 2-hydroxyethyl butyl carbamate, 202 g (2.8 moles) acrylic acid, 350 g toluene (37 % by weight of the reacting mixture), 500 ppm on end product methyl ether hydroquinone (MEHQ), and 0.1 % on end product HSPO2. PTSA (p-toluenesulfonic acid, 70 g) was added to reach an end concentration of 18 % mol on starting hydroxyalkyl carbamate. An air sparge was injected to prevent gelation. Pressure was reduced in the reaction vessel to about 350MMHG in order to allow reflux of a toluene/water azotrope. The mixture was heated to 70°C and stirred until no more water was distilled over. After 6 hours, 33 g (77 % of the theoretical value) of esterification water was collected in the Dean Stark. 2/Work-up When no more water was distilled over, the mixture was cooled to 60°C and neutralized by the addition of 140 g of a 50% solution of NAOH in water. This mixture was washed three times with 20 % by weight of the reacting mixture with water containing 20 % NaCl, dried via azeotropic distillation with air sparging to remove all the water and finally filtered. The toluene was distilled and stripped under vacuum (30 mmHg) to remove all traces of toluene. Air was sparged to prevent POLYMERIZATION/GELATION.
References:
WO2004/52843,2004,A1 Location in patent:Page 35

13105-54-9
12 suppliers
inquiry
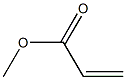
292638-85-8
2 suppliers
inquiry
![2-[[(BUTYLAMINO)CARBONYL]OXY]ETHYL ACRYLATE](/CAS/GIF/63225-53-6.gif)
63225-53-6
34 suppliers
$63.89/100ml
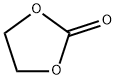
96-49-1
484 suppliers
$6.00/100g
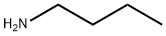
109-73-9
439 suppliers
$9.00/1g
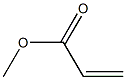
292638-85-8
2 suppliers
inquiry
![2-[[(BUTYLAMINO)CARBONYL]OXY]ETHYL ACRYLATE](/CAS/GIF/63225-53-6.gif)
63225-53-6
34 suppliers
$63.89/100ml
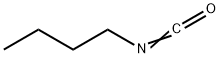
111-36-4
196 suppliers
$41.00/5ml

818-61-1
472 suppliers
$6.00/25g
![2-[[(BUTYLAMINO)CARBONYL]OXY]ETHYL ACRYLATE](/CAS/GIF/63225-53-6.gif)
63225-53-6
34 suppliers
$63.89/100ml