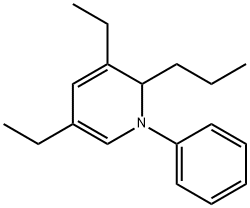
3,5-Diethyl-1,2-dihydro-1-phenyl-2-propylpyridine synthesis
- Product Name:3,5-Diethyl-1,2-dihydro-1-phenyl-2-propylpyridine
- CAS Number:34562-31-7
- Molecular formula:C18H25N
- Molecular Weight:255.4
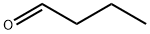
123-72-8
439 suppliers
$12.32/25ML
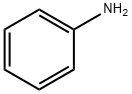
62-53-3
684 suppliers
$10.00/1g
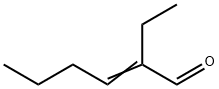
645-62-5
87 suppliers
$6.00/5g
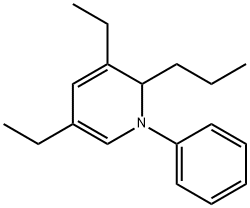
34562-31-7
121 suppliers
$40.00/1g
Yield:34562-31-7 69.8 %Chromat.
Reaction Conditions:
Stage #1: butyraldehyde;anilinewith acetic acid at 75; for 5 h;
Stage #2: with sodium carbonate in water; for 5 h;Product distribution / selectivity;Heating / reflux;
Steps:
III.4
EXAMPLE III; Several parameters were changed between Example I and Example II. To isolate the effects of each parameter, a series of runs was made wherein in each run only one parameter was changed. As shown in Table 1, runs were made to compare the reaction temperature after completion of the addition of the reactants and the effect of neutralizing the reaction mixture prior to refluxing. All reported yields are based on the weight of the recovered top layer from the reaction mixtures and a gas chromatograph (GC) analysis of the top layer. Thus, these are chemical yields of DHP made and not isolated recovered yields.Runs 1, 2, and 3 are a comparison of reaction temperature after the addition of the reactants. In run 1 the reaction was immediately heated to reflux, in run 2 the reaction was immediately heated to 75° C., and in run 3 the reaction was held at <45° C. for one hour before heating to 75° C. No difference in chemical yield was seen between runs 1 and 2. However, subsequent recovery of DHP from the crude mixture was greater with DHP prepared according to run 2 (data not shown), perhaps due to a decrease in the production of other compounds that make purification more difficult. In run 3, an improvement in the chemical yield of DHP was seen in addition to the improvement in recovery during subsequent purification. Thus, it has been found that holding the reaction mixture at a lower temperature for a period of time is beneficial to formation and purification of DHP. Without being bound to any particular theory, it is thought that the lower temperature may suppress the formation of other products that consume materials that could have been converted to DHP. Runs 4 and 5 are comparisons of the effect of base neutralization prior to refluxing on DHP yield. Previous work had shown DHP to decompose under acidic conditions when heated, especially at high temperature. By neutralizing the acidic catalyst before heating to reflux temperatures, decomposition of DHP can be suppressed. No difference in DHP chemical yield was seen in runs 4 and 5 but, again, subsequent recovery of DHP from the crude mixture was greater with DHP prepared according to run 4 than with run 5 (data not shown). Neutralization with a base allows the excess butryaldehyde to be reduced via base-catalyzed self-condensation, which is faster than acid catalyzed self-condensation. Also, the base neutralized run appeared to give improved layer separation. The top layer was relatively clear as compared to the other runs in which the top layers were cloudy. It was also noted that top layers from the non-neutralized runs would form small water droplets or layers in the sample bottles after standing for a few days. Neutralization of the acid catalyst is particularly useful when the product is distilled under high temperatures. Distillation of a neutralized DHP crude mixture produces fewer decomposition products and leads to increased recovered yields of purified DHP.
References:
US2006/178517,2006,A1 Location in patent:Page/Page column 3
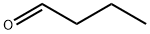
123-72-8
439 suppliers
$12.32/25ML
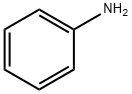
62-53-3
684 suppliers
$10.00/1g
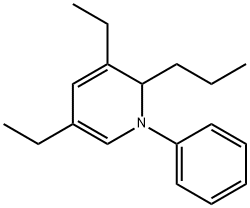
34562-31-7
121 suppliers
$40.00/1g
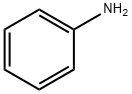
62-53-3
684 suppliers
$10.00/1g
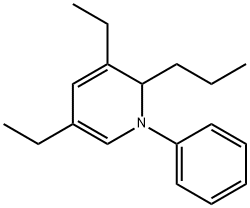
34562-31-7
121 suppliers
$40.00/1g

7732-18-5
496 suppliers
$13.50/100ML
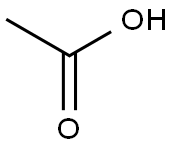
64-19-7
1600 suppliers
$10.00/25ML
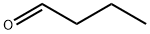
123-72-8
439 suppliers
$12.32/25ML
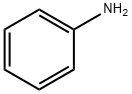
62-53-3
684 suppliers
$10.00/1g
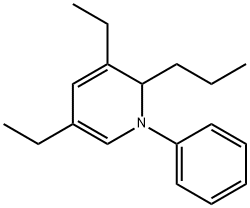
34562-31-7
121 suppliers
$40.00/1g