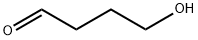
4-hydroxybutanal synthesis
- Product Name:4-hydroxybutanal
- CAS Number:25714-71-0
- Molecular formula:C4H8O2
- Molecular Weight:88.11
literature source US04064145
201230-82-2
1 suppliers
inquiry

107-18-6
0 suppliers
$24.60/100ml

38433-80-6
3 suppliers
inquiry
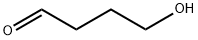
25714-71-0
43 suppliers
$195.00/100mg
Yield:25714-71-0 54.99% ,38433-80-6 34.7%
Reaction Conditions:
with (Sa)-1,16-bis(diphenylphosphino)-6,7,8,9,10,11-hexahydrodibenzo[b,d][1,6]dioxacyclododecine;hydrogen in toluene under 9308.91 - 10343.2 Torr;Autoclave;Overall yield = 91.27 %;Reagent/catalyst;
Steps:
2 i. Hydroforniylation Conditions
General procedure: [0060] The hydroformylation experiments were carried out in anhydrous toluene with the stoichiometry determined by the amount of Rh. In a typical experiment, a rhodium complex ( 1 equivalent, 4.3 χ If)"5 moles) was added to this solution of dry degassed toluene (15 g) and the desired phosphine ligand. This solution was then transferred to a 50 mL Parr autoclave. The autoclave was then flushed three times with a 1 : 1 CO/H2 mixture, and pressurized to 180 psi (1240 kPa), and the autoclave was heated with stirring, to the indicated temperature, for example 80 °C. Once the desired temperature was stably attained for at least 5 minutes, allyl alcohol (3.5 mL) was then injected and the autoclave pressure increased to 200 psi (1,379 kPa) with the CO:H2 mixture. The reactor was then maintained at a constant 200 psi (1 ,379 kPa) pressure and the gas uptake with time was monitored until there was no further gas uptake. The reactor was cooled down, depressurized and the solution was analyzed by gas chromatography to determine the products of the reaction, which included HBA, MHPA and C3 products, (n-propanol and Propionaldehyde). Results are shown in Tables 2 and 4.
References:
LYONDELL CHEMICAL TECHNOLOGY, L.P.;WHITE, Daniel, F.;MANDIMUTSIRA, Beaven, S. WO2017/79171, 2017, A1 Location in patent:Paragraph 0061
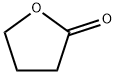
96-48-0
0 suppliers
$21.10/25g
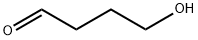
25714-71-0
43 suppliers
$195.00/100mg

50-00-0
891 suppliers
$10.00/25g

107-18-6
0 suppliers
$24.60/100ml

38433-80-6
3 suppliers
inquiry
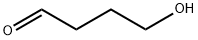
25714-71-0
43 suppliers
$195.00/100mg

1191-99-7
346 suppliers
$10.00/10g
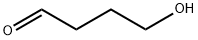
25714-71-0
43 suppliers
$195.00/100mg
201230-82-2
1 suppliers
inquiry

107-18-6
0 suppliers
$24.60/100ml
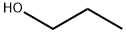
71-23-8
793 suppliers
$12.00/100g

38433-80-6
3 suppliers
inquiry
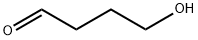
25714-71-0
43 suppliers
$195.00/100mg
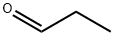
123-38-6
458 suppliers
$14.00/5mL