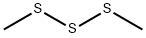
Dimethyl trisulfide synthesis
- Product Name:Dimethyl trisulfide
- CAS Number:3658-80-8
- Molecular formula:C2H6S3
- Molecular Weight:126.26
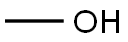
67-56-1
737 suppliers
$9.00/25ml

74-93-1
120 suppliers
$454.02/5MG
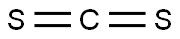
75-15-0
239 suppliers
$40.00/100g
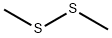
624-92-0
311 suppliers
$26.39/5ml
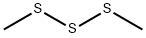
3658-80-8
243 suppliers
$34.00/5g
Yield:624-92-0 94.9%
Reaction Conditions:
Stage #1: methanol;methylthiolwith hydrogen sulfide;aluminum oxide with 14percent by weight of potassium tungstate at 400;
Stage #2: with sulfur;N-cyclohexyl-cyclohexanamine
Steps:
1 1. Example in a Continuous Experimental Plant
The two-stage dimethyl disulfide (DMDS) synthesis was carried out in a continuously operating laboratory apparatus which comprises all components of the flow diagram (FIG. 1). [00054] The MeSH tubular reactor (600 mm long, 25 mm in diameter) was filled with a self-prepared catalyst of aluminum oxide with 14% by weight of potassium tungstate. At a temperature of 400° C. (middle of the reactor) and a pressure of 1.1 barabs 48 g/h (1.5 mol) of gaseous methanol, 34 g/h (1 mol) of hydrogen sulfide and 40 g/h of back gas from the reaction column (composition: 72% of H2S, 12% of MeSH, 16% of dimethyl sulfide (DMS), small amounts of methanol and dimethyl ether) were fed into the tubular reactor. The gas composition at the reactor outlet was: 13.0% of H2S, 50.8% of MeSH, 10.3% of DMS, 21.6% of H2O, 2.4% of MeOH, 1.2% of dimethyl ether (DME). [00055] This gas enters the lower section of the reaction column (bubble-cap column containing 20 plates) and flows countercurrently to the downwardly flowing sulfur solution (still solution from distillation column, to which 19 g/h of sulfur and 0.1 g/h of dicyclohexylamine is metered in), where MeSH reacts with formation of H2S. The gas exiting at the top of the column and having the composition above is compressed, as back gas, and returned to the MeSH tubular reactor, where a relatively small proportion of the gas is removed from the system. The still solution heated to about 90° C. is two-phase, the upper phase being the water formed in the MeSH synthesis. The phases are passed to a phase separator, where they are separated and the upper, aqueous phase is collected in a discharge container (26 g/h). The lower organosulfur phase is passed at the side to a distillation column which is operated at subatmospheric pressure (300 mbar). The product DMDS was isolated in a sidestream takeoff (53 g/h) and had a purity of 99.6% (0.1% of dimethyl trisulfide, 0.3% of low-boiling components such as dimethyl sulfide (DMS), MeSH, CS2). The yield of DMDS, based on the sulfur used, is thus 94.9%. The low-boiling components produced at the top of the distillation column were in this case not recycled to the top of the reaction column as in FIG. 1.
References:
US6686506,2004,B1 Location in patent:Page column 5

74-93-1
120 suppliers
$454.02/5MG
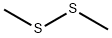
624-92-0
311 suppliers
$26.39/5ml
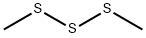
3658-80-8
243 suppliers
$34.00/5g
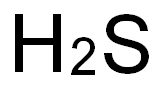
7783-06-4
69 suppliers
$158.00/25ml
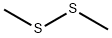
624-92-0
311 suppliers
$26.39/5ml
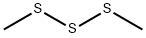
3658-80-8
243 suppliers
$34.00/5g
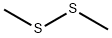
624-92-0
311 suppliers
$26.39/5ml
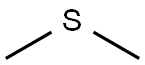
75-18-3
388 suppliers
$19.00/25mL
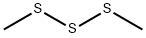
3658-80-8
243 suppliers
$34.00/5g
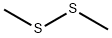
624-92-0
311 suppliers
$26.39/5ml

74-93-1
120 suppliers
$454.02/5MG
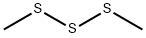
3658-80-8
243 suppliers
$34.00/5g
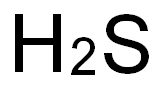
7783-06-4
69 suppliers
$158.00/25ml