
Tetrapropoxysilane synthesis
- Product Name:Tetrapropoxysilane
- CAS Number:682-01-9
- Molecular formula:C12H28O4Si
- Molecular Weight:264.43
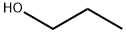
71-23-8
749 suppliers
$12.00/100g

682-01-9
208 suppliers
$22.00/25mL
Yield:682-01-9 78.7%
Reaction Conditions:
with silica gel;potassium hydroxide at 210; under 11251.1 Torr; for 6 h;Autoclave;Inert atmosphere;
Steps:
14 Example 1
General procedure: (0055) To the upper portion of a 200 mL autoclave (manufactured by Nitto Koatsu Co., Ltd.) made of SUS 316 and equipped with a mechanical stirrer, a tube made of SUS 316 and having an inner diameter of 4.6 mm, which tube is to be used as the outward flow path (corresponds to the portion indicated as 108 in the FIGURE) for allowing the vaporized component of the reaction mixture to move therethrough, and is configured to be able to be heated using a ribbon heater, as well as a tube made of SUS 316 and having an inner diameter of 4.6 mm, which tube is to be used as the inward flow path (corresponds to the portion indicated as 109 in the FIGURE) for allowing a component which has been brought into contact with the molecular sieve to move therethrough, were connected. The temperature (T2) in the pipe of the outward flow path was maintained at 249° C. during the reaction. To these tubes, a 30 ml portable reactor (manufactured by Taiatsu Techno Corporation) made of SUS and containing 25 g of Molecular Sieve 3A (in the form of 2 mm beads, manufactured by Merck KGaA) was further connected. Constant temperature water was allowed to circulate around the exterior of the portable reactor, so that the temperature (T1) of the molecular sieve portion inside the portable reactor was maintained at 53° C. A quantity of 0.9 g of a silicon dioxide (Wako gel 60N, from 63 to 212 μm; manufactured by Wako Pure Chemical Industries, Ltd.), 80 g of ethanol and 0.008 g of potassium hydroxide were introduced into the autoclave. Subsequently, an argon gas was fed from a gas cylinder at a temperature of 25° C., to fill the autoclave such that the pressure therein as indicated by a pressure meter (PGC-50M-MG10; manufactured by Swagelok Company) was 0.75 MPa. The autoclave was then maintained for 10 minutes while stirring, and sealed. Thereafter, the autoclave was heated to 240° C. (T1) while stirring the interior of the autoclave at 500 rpm, and the reaction was allowed to proceed for six hours. The yield of the resulting tetraethoxysilane based on silica was 72.5%. The reaction results are shown in Table 1.
References:
US2020/347082,2020,A1 Location in patent:Paragraph 0055; 0068; 0073
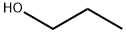
71-23-8
749 suppliers
$12.00/100g
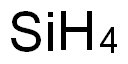
7440-21-3
205 suppliers
$30.00/100gm

682-01-9
208 suppliers
$22.00/25mL
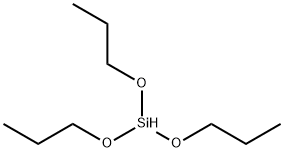
6485-85-4
0 suppliers
inquiry

682-01-9
208 suppliers
$22.00/25mL